New York has 123 homes constructed under the environmentally friendly “passive house” building standard certified by Passive House Institute US. But architects and environmental experts say it should become the norm, especially for affordable projects in New York City.
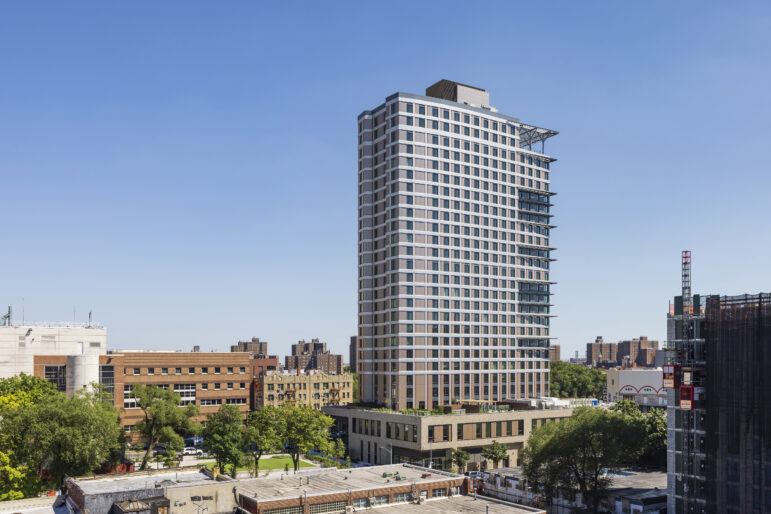
Albert Vecerka/ESTO
425 Grand Concourse, in the Bronx, an affordable project by Dattner Architects and Trinity Financial, deemed the largest certified passive house project in North America.
Draped in shiny metal panels and tall windows, anyone walking by 425 Grand Concourse in the Bronx could mistake it for a luxury apartment complex. But the 26-story facility is actually an affordable housing project built for low to middle-income families.
Inaugurated in June of last year, the project was commissioned by the city’s Department of Housing Preservation (HPD) and developed by Trinity Financial and Dattner Architects. It boasts amenities like a rooftop garden, a gym, an event space and laundry rooms on every floor.
But its most notable quality: it holds the title of largest certified passive house project in North America.
Passive house is an environmentally friendly international building standard that uses design elements like insulation, airtightness and heat recovery to consume less energy. By saving energy, buildings emit fewer greenhouse gasses and deliver lower utility bills. These constructions also boast superior air quality, producing a healthier environment for residents.
“People who live in affordable housing need to be able to reap those benefits,” said Shefali Sanghvi, Dattner Architects’ director of sustainability.
But most developers, she said, still consider passive house standards a “boutique” concept, reserved for upper-class residences like the Convivium on East 86th Street and Flow Chelsea on West 29th Street.
There are 123 passive house certified projects in New York state, according to the certification system Passive House Institute US (PHIUS). In the city, 50 affordable passive projects have been financed or are in development, according to HPD.
Architects who spoke to City Limits said passive house is starting to catch on in New York, but it’s still far from being the go-to construction model. The building industry is skeptical of investing in such projects, which are also still difficult to secure funding for.
But with the Climate Act seeking to cut New York’s greenhouse gas emissions 85 percent by 2050, passive housing development can both benefit tenants and help the state reach its climate goals, according to John Woelfling, head architect for 425 Grand Concourse.
The buildings’ 276 rent controlled apartments are considered affordable under the city’s standards for households earning between $30,000 to a little over $130,000 a year, including 28 units reserved for formerly homeless individuals.
“I see passive house as one way to address the twin crises we are facing: affordable housing and the climate crisis,” Woelfling said.
Why go passive?
The passive house standard was originally developed in 1990 by the Passive House Institute (PHI) in Germany. The Passive House Institute US (PHIUS), founded in 2007, later became another certification system widely used in the United States.
There are currently 840 certified passive house projects in the country. There could be many more—but architects say most developers prefer a different model.
“Buildings today hide their mistakes by using oversized mechanical systems. And they use more energy than they should as a consequence,” Ken Levenson, executive director at the non-profit Passive House Network, told City Limits.
Instead of opting for these “active systems,” Levenson explains, the passive house standard uses a “passive” approach that seeks “to get away from the gadgets and have the building’s structure itself drive the performance of the building.”
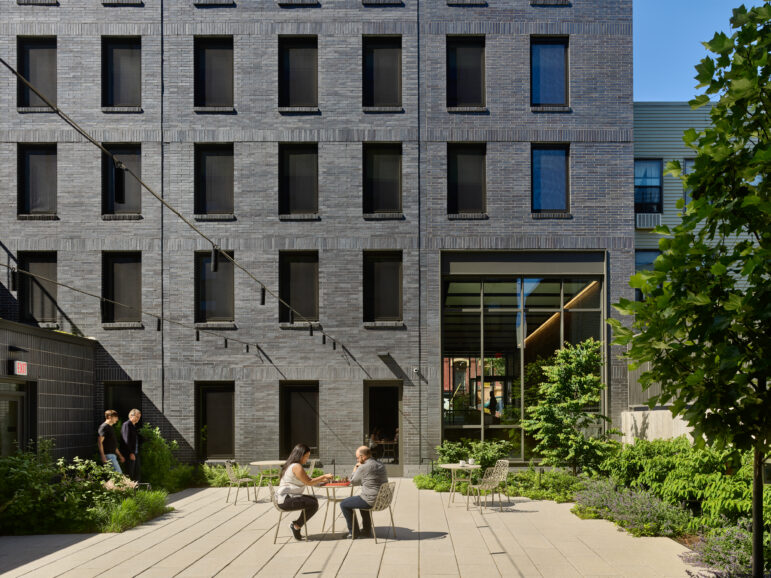
Breaking Ground/Frank Oudeman
Breaking Ground’s Betances Residence in the South Bronx, the group’s first passive house project for seniors.
Passive houses have an air-tight building envelope that controls and maintains the inside temperature comfortably for longer, a lot like a thermos that keeps your drink cool in the summer and warm in the winter. Using a building’s heating and cooling systems less often saves energy and drives down utility costs, an important feature for low-income households that can’t afford astronomic energy bills.
Passive house sites can save up to 85 percent on heating and cooling costs and up to 60 percent on total energy use compared to a conventional construction, according to a report by HPD in partnership with other nonprofits.
The buildings also have well-insulated windows that keep heat or cool air from escaping, and pay particular attention to solar gain—using a building’s orientation and window size to take advantage of natural light.
Another key component is what experts call a “balanced” ventilation system to allow fresh air into the building while retaining pre-conditioned heating or cooling. This process filters the air and produces better air quality, which can be particularly important for disadvantaged communities: A 2021 study found that on average, people of color are disproportionately exposed to the air pollutant PM 2.5, which is responsible for 85,000 to 200,000 excess deaths a year in the United States.
Another study by the research hub Rocky Mountain Institute found that lower income communities and communities of color tend to live closer to “polluting sources such as highways, power plants, toxic waste sites, and landfills.” These exposures, the study adds, “contribute to a variety of health conditions, from asthma to low birth weights to premature mortality.”
Yu Ann Tan, a senior researcher at the Rocky Mountain Institute who studies the benefits that healthy homes have on low-income families, said improved air quality in homes helps to reduce “asthma, diabetes, hypertension, obesity, and kidney disease.”
“There are a ton of economic and social benefits that I think passive house can deliver that are particularly important for these communities that really need that kind of support,” Tan said.
But most developers who try to build sustainable projects are skeptical about going the passive route.
“There is conservative nature to the building industry. So you’ve got builders and architects who just do what they’ve always done, and then you have the real estate [companies] that only want to sell what’s been sold before,” Levenson said.
Last year, the Real Estate Board of New York celebrated some of the city’s most sustainable constructions, applauding passive house projects like Sendero Verde, a mixed income passive house-certified building developed by Jonathan Rose Companies.
But Levenson says these projects are frequently one-off achievements. When it comes to building passive house standards on a larger scale, “everybody’s dragging their feet.”
He believes legislators should find ways to offer more building incentives to make passive house the norm, and make changes to the building code to include passive house standards.
“Otherwise, passive house will just exist at the fringes at best,” Levenson added.
A question of money
Patrick O’Shei, director of market development at New York State Energy Research and Development Authority (NYSERDA), says one of the big challenges to implementing passive house on a wider scale is overcoming the building industry’s “familiarity bias.”
“[Developers and investors] are used to building a certain way, so there’s uncertainty about how hard it’s going to be to build something that they have never built before,” O’Shei told City Limits.
As a result, developers and investors often drive up costs for projects that involve passive house standards to make up for the risk of working with an unfamiliar model.
NYSERDA says it’s trying to change that through its Buildings of Excellence Program, which awards up to $48 million dollars to carbon-neutral-ready multifamily building projects in the state. The program, now in its third edition, helped fund passive house projects like the 425 Grand Concourse. But that state aid generally accounts for just a portion of costs.
“The challenge is that construction is incredibly expensive. So even if we’re providing more than a million dollars in a project with clean energy attributes, that might represent somewhere between 1 percent to 3 percent of the project cost,” O’Shei explained.
There is debate among architects and environmentalists about how much more a passive house project costs when compared to a conventional building. Sadie McKeown at the Community Preservation Corporation (CPC), a non-profit that works closely with city government to finance affordable projects that are also sustainable, said passive house costs between 5 and 10 percent more for a new construction.
“We’ve done a lot of work financing high performance and passive house buildings. But there’s limited money to support any kind of [sustainable] project,” McKeown said. “And so that makes it very, very challenging.”
Funding passive projects requires piecing together government incentives like tax abatements to offset the costs of building with sustainable materials, which are often imported from abroad, she added.
Other developers, though, say it’s not impossible to build both affordable and passive.
Nonprofit Riseboro, which claims to be among the city’s first to bring passive standards to affordable housing back in 2012, has built eight such projects to date, and did “all of them on budget,” said Ryan Cassidy, director of Sustainability and construction.
“We definitely are in the camp of saying that you can do it at the same cost,” said Cassidy.
Breaking Ground, another group that builds affordable homes for the unhoused, just completed its first passive house project last year for seniors who are exiting homelessness or living on very low incomes.
Elissa Winzelberg, the organization’s director of design and construction, said it’s starting to get easier to build passive projects more affordably. Until recently, many of the parts needed for the design, like the air-tight windows, were imported from places like Germany.
“Now they’re beginning to be manufactured here,” Winzelberg said. “The more this is done, more American manufactures will arise and the more cost effective and widespread the standard will become.”