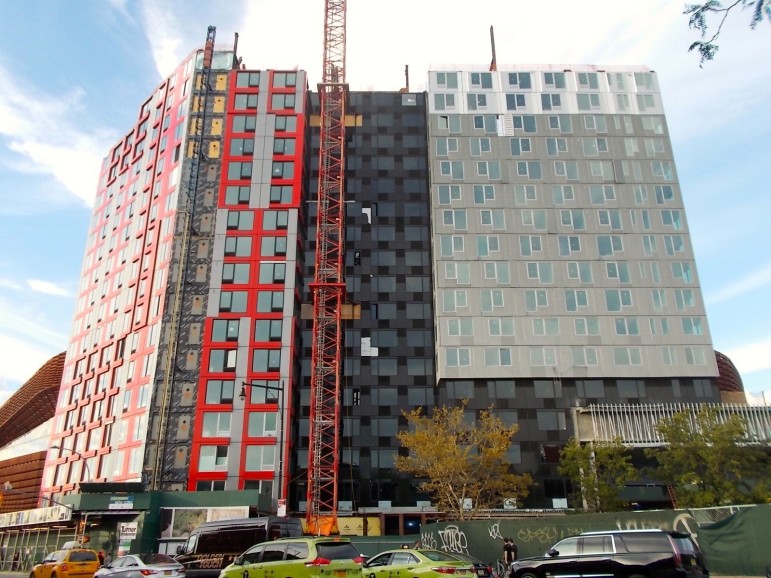
Norman Oder
The modular building known as B2, at 461 Dean Street, was supposed to cost less and be done much faster than a conventional high-rise. But problems in stacking the modules and keeping water out made for a slower, more expensive build-out.
The Atlantic Yards apartment tower known as B2 officially launched in December 2012 with great fanfare and high hopes, and not just because of what developer Forest City Ratner proposed to build: 32 stories housing 363 apartments, half of them affordable. It was that B2, nearly flush to the Barclays Center, would be the world’s tallest modular tower, with its flooring, fixtures, appliances, and facades delivered within a metal-framed chassis some 10′ high, 15′ wide, and 30′ long. Forest City said it had “cracked a code” and claimed an “iPhone moment”.
Two additional Atlantic Yards towers would start within the next 12 to 18 months, among the 6,430 apartments—2,250 of them below-market—planned for the project, all to be built modular. B2’s 930 mods—which Forest City CEO MaryAnne Gilmartin likened to “shrink-wrapped apartments—would be made at a new factory at the Brooklyn Navy Yard. The first mods arrived at Dean Street and Flatbush Avenue in December 2013 with a proud “Made in Brooklyn” wrapping.
B2’s pioneering approach was seen as more than just an intriguing development at the highly contested Atlantic Yards site. Its designers and admirers thought the modular method might lower the cost of affordable housing, creating a new model for high-rise, union built apartments.
Today, the reality of B2 has not matched the anticipation. The building—delayed, stalled, and since re-started to reach half its ultimate height—will take more than twice as long as promised and cost far more than projected. B2, also known as 461 Dean Street, remains mired in lawsuits filed by Forest City and its former partner Skanska, with dueling charges of incompetent execution and flawed design.
While Forest City Chairman Bruce Ratner in July 2014 claimed on NY 1 that modular “worked out technically perfectly,” with delays the only problem, state documents acquired via a Freedom of Information Law (FOIL) request paint a more ominous picture. Half of the first 39 apartments suffered significant water damage. The first four floors were “largely gutted,” according to reports from consultant STV, which serves as owner’s representative for Empire State Development (ESD), the state agency overseeing/shepherding the entire Atlantic Yards project, which has been renamed Pacific Park Brooklyn.
The builders got so skittish that, on the 9th and 10th floors, drywall sections of the ceilings and walls closest to the windows were omitted from mods, to be installed later, undermining the concept of completing as much as possible in the factory. (The STV documents—here’s an example—do not seem to bolster either side in the legal dispute between Forest City and Skanska.)
Mold was found at various places in the building and, at least according to the 2013-2014 documents acquired via FOIL, queries from STV about more mold—and the possibility of air monitoring—went unanswered by Forest City and Skanska for months. In response to City Limits’ inquiry, an ESD spokesperson said: “It is not uncommon for construction sites and building materials to be exposed to moisture while work is ongoing. When the ESD project team notified FCR that our owner’s representative had observed evidence of possible mold, FCR took appropriate actions to remedy the situation.”
While many in the modular field hail Forest City’s boldness, some wonder if the project pushed too hard, given the challenge of what builders call “tolerance issues”—essentially cumulative slight deviations from a precise fit—as the 32-story building rises. Modular apartment construction has begun to emerge in New York City with more tempered ambitions, notably the completed seven-story Stack in Inwood and the emerging 11-story Carmel Place in Kips Bay, a city pilot program for micro apartments.
Forest City, which declined to respond to specific questions for this article, is looking forward, not back. “Progress on B2 has been excellent since work resumed earlier this year and we are on track to complete the building next year,” spokesman Jeremy Soffin stated. “We remain enthusiastic about the potential for high-rise modular construction in New York.” ESD said it was “satisfied with the pace of construction on the B2 site.”
Grand ambitions
While modular builders in the United States have focused on low-rise structures including retail facilities and hotels, those abroad have been more ambitious. The tallest modular building was long a 24-story dormitory built in 2010 in Wolverhampton, England, though this year a 57-story building was completed in Changsha, China. Forest City’s plan to leapfrog Wolverhampton drew kudos from public officials like Mayor Mike Bloomberg, and many in the planning, housing, and construction fields for charting a new way.
“We think [modular] can be explosive for the business,” Forest City construction chief Bob Sanna told the trade publication Engineering News-Record before construction began. Forest City aimed to save 20 percent off conventional construction and cut 10 months from a 30-month schedule, thanks to concurrent work both on-site and in the factory. Beyond savings from speed, a new labor agreement meant cross-trained union workers would complete multiple tasks at lower wages in climate-controlled conditions. Building some 60 percent of B2 off-site would mean greater quality control, require fewer trucks, and produce less waste.
New York magazine architecture critic Justin Davidson, in his magazine’s end-of-2011 “Reasons to Love New York” issue, cited the soaring skyline, including the coming “world’s tallest modular tower,” designed by SHoP, which had redesigned the Barclays Center. By contrast, Brooklyn architect Jim Garrison, a modular veteran who served as a consultant to a former Forest City contractor, cautioned in October 2011, “The American modular industry typically builds up to four stories. It has not yet built a 30-plus-story modular tower or anything nearly that tall. The challenges are those of engineering, assembly, and production.”
Building “quickly, densely, affordably, and sustainably,” wrote Gilmartin in the Forum for Urban Design’s spring 2013 Next New York compilation, could help “radically shift how we build great cities.” Modular, Gilmartin said at the Municipal Art Society’s (MAS) October 2013 Summit for New York City, “will be truly revolutionary,” and would “significantly help” with affordable housing. In 2014, the MAS would award Ratner and Gilmartin its highest honor, the Jacqueline Kennedy Onassis Medal, for achievements including modular.
Problems mount
Forest City was “besieged” with interest from other developers, Gilmartin in March 2014 told a real-estate audience. “We will take competitor business into the factory,” she declared, “but right now the quest is to get this building up.”
Indeed, that quest faced complications. For nearly a year, STV’s William King had been reporting to Empire State Development about delays. Though the FC Skanska joint venture aimed to reduce construction time from one month per floor to one week, on Dec. 13, 2013, one day after the first modules were set in front of invited media, King noted that the initial floor had taken more than four months.
In March 2014, three installed mods on the third floor were removed for repairs to gaskets, which seal the facade, thus delaying fourth-floor installation, King reported. Other mods would have to be reinstalled, as well. Though second-floor mods were said by FC Skanska to be finished, King’s walk-through at B2 revealed that many lacked appliances, sinks and toilets. Some had unfinished flooring and wall work. Also required was “on-site leak-damage repair/replacement of water-damaged ceilings, walls and floors, and possibly other elements such as electrical,” he wrote.
Third-floor mods he observed appeared “substantially complete,” but fourth-floor mods at the building were “in a more raw state.” King spotted evidence of leaks from gaps between mods and the brace frame. Some mods “were a tight fit,” he wrote, adding, “Reportedly have had to shave drywall in past in order to squeeze in mods, then caulk.”
On April 4, 2014, King reported that, after a very rainy weekend, “a rain barrel filled up” in one third-floor unit, and water entered second-floor mods. A revised schedule pushed back completion to May 2015, though King was doubtful. Indeed, on April 19, 2014, as evidence of the slow progress mounted, with just 122 modules installed, Forest City acknowledged to the New York Times that B2 was delayed until late 2015.
By then, Forest City was pulling back on its modular ambitions. Its incoming partner on Atlantic Yards (excluding B2 and the arena), the Shanghai government-owned Greenland Group, had decided the next three towers would be built conventionally. That decision seemed a recognition of the delays at the factory because of the ongoing B2 project, and a red-hot Brooklyn market into which the joint venture was anxious to dive more deeply. It meant Forest City wouldn’t necessarily be able to build steadily on the lessons of B2.
Forest City claimed to the Times that it had solved modular’s technical challenge but cited delays in setting up the factory, cross-training workers, and establishing supply lines. Internal reports from the owner’s representative suggested larger challenges. King that month reported on gut renovation of wall board from ceilings and walls on the second floor, as well as “significant water damage” in half the units. “Jury is still out on gaskets which may be under increasing stress under weight of additional floors,” he wrote April 8, 2014. Four months later, in the last of the documents delivered by FOIL, he had not reached a conclusion.
Over the late spring and summer, more water damage emerged, as well as quality control issues, including torn gaskets, dents, and scratches to the exterior façade. One mod was such a tight fit, King reported in June, that a worker used a crowbar to try and move it.
“The third worst occurrence of leaks into the building occurred after a heavy rainstorm” on July 2, 2014, King reported. Workers had to rip out the ceilings and walls of one sixth-floor unit, while water infiltration was noted in other units. Representatives of Skanska and MG McGrath, the facade contractor, “were at a loss as to how water got into the building,” King reported. By then, the ninth and tenth floors were being installed with some drywall sections omitted. On Aug. 1, 2014, King noted that all the floors, from 2 through 8, “have suffered significant water damage.”
If such problems weren’t visible to passersby, others were glaring. As shown in July 12, 2014 video shot by this reporter, loose facade panels flapped loudly in the wind. Some modules didn’t line up precisely enough for the facades to fit, so panels had to be wired open, King wrote.
But as problems mounted, bi-weekly construction updates provided by the developer and distributed by ESD made no mention of the building’s problems or the ad hoc repair work, which also included re-lifting installed units to ensure proper alignment. Nor did state officials—long navigating the potentially awkward role of both overseeing and shepherding the project—bring such problems to light.
Conflict emerges
The internal construction reports provided via FOIL end in September 2014 – just after a simmering dispute between the modular partners finally became public. Skanska shuttered the modular plant and furloughed workers, having failed in its request for Forest City to pay more to cover the added costs of delays and construction problems. (Forest City says Skanska should abide by a fixed-price contract, while Skanska counters that the risk it assumed was based solely on a failure to follow Forest City’s intellectual property.) The two companies each claimed to have been blindsided, Skanska by Forest City’s decision to build the next towers conventionally and Forest City by Skanska’s closure of the factory.
As later surfaced in the litigation, a 146-page letter from Skanska’s Richard Kennedy warned that, beyond the risk of leaks, the steel frames used in the project had limited adjustability, threatening misalignment. While a 2012 prototype had tested well, Kennedy contended that two-story model couldn’t capture the strains and stresses on a full, high-rise building. Forest City called such criticism baseless and blamed Skanska’s execution as general contractor.
After an emerging modular builder, Julian Bowron of VectorPraxis, told WNYC last October that some modules of B2 seemed visibly misaligned, a Forest City spokesman said it was unprofessional to inspect an incomplete building. “It was self-evident there was a problem,” Bowron, a machinist by training, said recently.
Skanska asserts that “large parts” of the cost overruns are attributable to the challenge of bringing mods into alignment. Ryan Smith, who directs the Integrated Technology in Architecture Center at the University of Utah, noted that many conventional buildings require adjustments, and modular buildings can face tolerance issues, “but at that height that’s going to be exacerbated.”
After being read King’s report of “significant water damage,” Smith (who has no direct experience with B2), said that’s “not very common” with modular.
A new start
As the lawsuits percolated and cost overruns mounted, Forest City (having bought out Skanska) in early 2015 reopened the Navy Yard factory under its own management, determined to finish B2 and maintain its modular business, which cost $6 million in research and development, not to mention the cost of the factory. The tower, once expected to cost $155 million, could ultimately cost $265 million, Forest City told the Securities and Exchange Commission. It’s now scheduled to open by December 2016, a four-year buildout. Forest City last October bought out the interest of its 75 percent equity partner, the Arizona State Retirement System.
Construction updates prepared by Forest City and circulated by ESD hint at ongoing challenges with the building. This past March, an update acknowledged the need to “[tighten] up the tolerances of the 10th floor modules,” before higher floors could be added, including “possibly lifting some modules with the crane and re-setting.”
Forest City, whose executives are close to Mayor de Blasio, still thinks modular can help solve affordable housing challenges. As Crain’s New York Business noted in March, the city has proposed zoning changes that would increase the height—but not square footage—limits on buildings, which would assist modular buildings, since the stacked units mean much thicker floors than in conventional buildings.
Since construction resumed, Forest City has welcomed factory visitors. “The pace of construction at the factory is really impressive,” declared former ESD CEO Kenneth Adams at a July 28, 2015 meeting of the Atlantic Yards Community Development Corporation, an advisory body he heads. The “workforce development,” he said, was “really compelling and very positive,” citing “200 people working, with good wages and benefits, 11 percent women… 85 percent people of color.”
It’s not clear that the troubles encountered by B2 reflect on the potential for high-rise modular in general, the specific technology used in the project, or the execution by the companies involved. Some in the field criticized Forest City for pushing modular beyond typical North American practice by commissioning modules with their facades attached in the factory, which shows a greater commitment to prefabrication but allows for less adjustability. Bowron praised Forest City for trying “the most progressive possible way,” following the lead of builders in Australia and Europe.
“What we do know about this project is that it was ‘unconventional’ even for the modular industry,” observed Tom Hardiman, executive director of the Modular Building Institute, a trade group, after the stall last August. “The developer chose to create a new modular company with the contractor, rather than working with established and experienced modular manufacturers (including one located in Brooklyn).”
Still, MBI is enthusiastic, recently tweeting a picture of the building, stating “History in the making!”
The ongoing lawsuit and murkiness from the developer and state may leave lingering questions about what happened in B2. Once the building is approved for occupancy, Smith says, people “should have some confidence this project is going to perform well,” said Smith, who calls B2 “very innovative” but suggests Forest City might have aimed too high, too fast. “Doing the tallest building maybe wasn’t the best method.”
The full set of documents is here.